9 handy tips for industrial machine maintenance
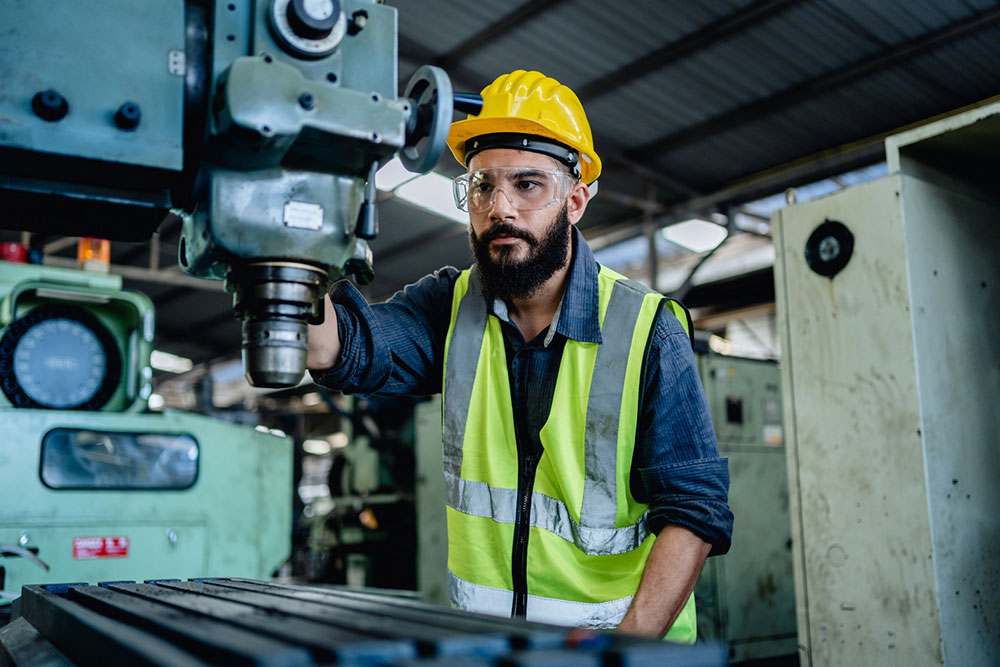
The manufacturing industry is an important part of society today. Further, with increasing consumerism, there is a continuous demand for quality products, which have to be made available in a timely manner. This has been made possible with the use of high-tech machines. However, machine maintenance is not easy and often involves considerable time, money, and resources. To help one ensure the smooth functioning of their equipment, here are tips for hassle-free industrial machine maintenance:
1. Check lubrication levels regularly
One of the most common reasons why industrial machines break down is friction. To avoid this issue, one must regularly check machines’ lubrication levels, particularly around high-speed spindles and motors, and keep them well-oiled. Additionally, one must ensure that the right type of lubricant is used for each machine. One can check the user manual or manufacturer’s recommendations and follow the specified directions closely to get the most out of the machine.
2. Clean the machines daily
In an industrial setting, dirt and dust can quickly accumulate. This can cause corrosion or rust, leading to malfunctions and breakdowns. To avoid this, the machines must be cleaned every day with an appropriate cleaning solution. One should also pay special attention to the cracks and crevices during cleanup. Once done, one should apply industrial rust preventative to metal surfaces or parts.
3. Set up a machine inspection schedule
One should set up a regular inspection and maintenance schedule for all machines. This must be available to all the machine operators so they can keep tabs on the efficiency. Additionally, any safety mechanisms on the machine must be checked regularly to ensure that they are in working condition. These mechanisms could be emergency shut-off buttons, warning signs, and guard rails. Failure to inspect the machinery can increase the threat to life and property if the equipment malfunctions.
4. Perform calibration checks
When using machines involved in highly precise tasks, it is important to pay attention to the calibration. This can help assure the operator that the machine is working correctly and efficiently. The frequency of calibration checks should be governed by the type of machine being used. One can speak to the manufacturer or technician for more details regarding the machine.
5. Maintain a log
Maintaining a log of the machine’s use, performance, inventory numbers, failures, shortages, safety incidents, uptime, and maintenance is an important step. It allows owners to keep track of the machine’s performance and identify any areas of concern. One should consider noting down details like when the machine was last used, the type of maintenance or repair it has undergone, and probable issues that may arise, among other updates. This information can be crucial in helping recognize issues before they turn into serious problems.
6. Adopt a software-based maintenance system
Many industrial plants continue to rely on paper reports. This can significantly fill up the storage space. Here, one can try switching to a computerized maintenance monitoring system (CMMS) designed to help employers and managers keep track of completed work, maintenance logs, machine downtime, and other information in real-time. Companies can also opt for systems with additional features, such as smart sensors to detect rust, temperatures, and corrosion, unmanned aerial vehicles (UAVs) and drones, robotics, IoT-connected sensors, artificial intelligence, and machine learning.
7. Educate the staff on maintenance
Employees and operators who handle the machine regularly must be fully aware of basic maintenance guidelines and technical know-how required to operate the machine safely. They should be aware of what to look for in terms of product quality and output quantity and be able to recognize glitches in the process. The staff must be trained thoroughly before they begin handling these machines. They must also be offered ongoing training to keep them up to date on the latest best practices for safe and effective handling. Failure to do so may result in unexpected downtime or an increased likelihood of breakdowns and malfunctions.
8. Keep spare parts on hand
Minor repairs, such as consumables like filters, can be undertaken on-premises by keeping an inventory of basic spare parts on hand. One can speak to the manufacturer or an independent technician to determine the parts that can be stored
9. Formulate a backup plan
Production can take a big hit if critical machines are impacted. To ensure that efficiency is not compromised, companies must have a contingency plan in place for sudden machine breakdown. They should also train the staff regarding these procedures.